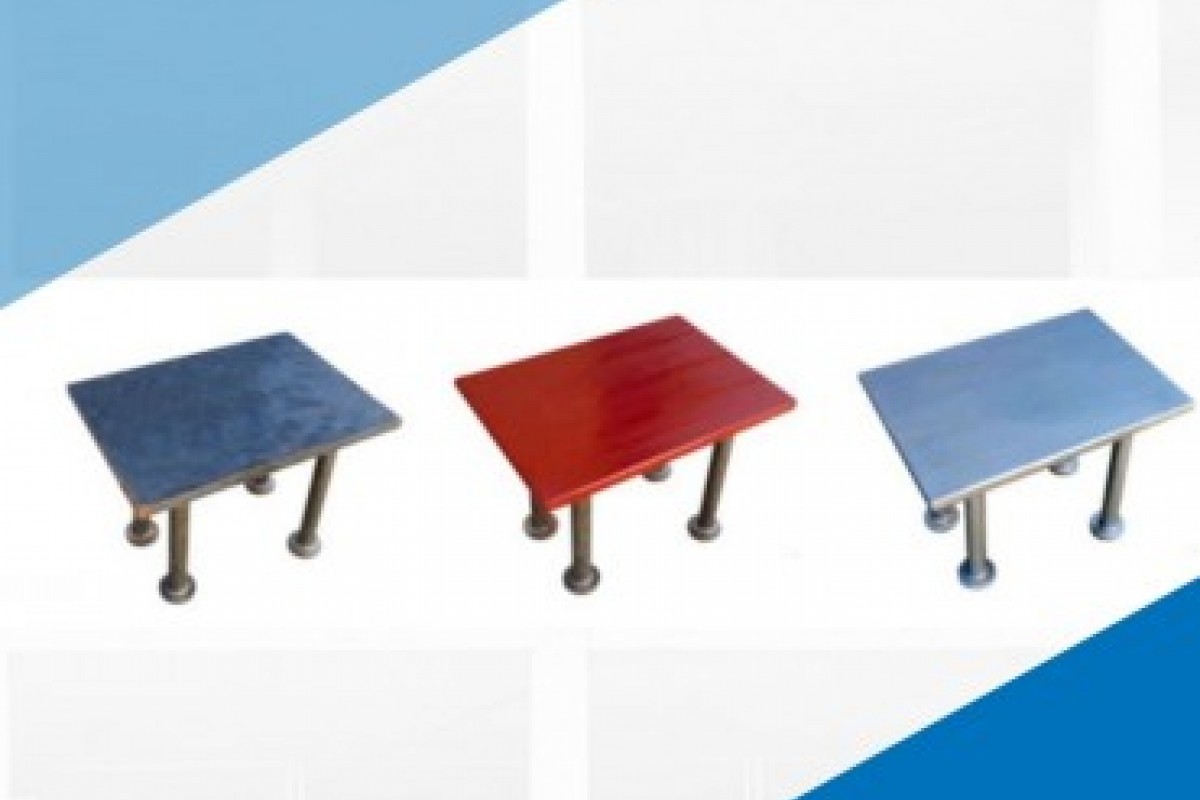
Noxifer offers a wide range of products for the precast concrete industry with different surface treatments depending on the exposure class to corrosion
Every engineer, architect or calculator knows that the fact of sizing any metallic element to resist the efforts to which it is subjected is crucial in your project. In addition to this aspect, it is also decisive to choose the correct surface finish or the type of steel depending on the element's corrosion exposure class.
At Noxifer we collaborate in many engineering and architecture projects in which we supply construction accessories with different surface treatments and/or types of steel according to the restrictions of each particular situation. To show an example, the current Noxifer catalog shows a table of the entire range of products and the possible surface treatments and steels that are available so that customers can easily find which is the most suitable option for their project.
The different options offered by Noxifer are detailed below:
- Finish without additional protection
- Electrolytic zinc plating according to UNE-EN ISO 2081
- Galvanized Steel Sendzimir DX51D + Z275 according to UNE-EN 10346
- Hot dip galvanized according to UNE-EN ISO 1461
- AISI 304 Stainless Steel
- AISI 316 Stainless Steel
In addition, the same catalog shows two tables of durability of the pieces depending on the surface finish and the type of stainless steel that have been made following the indications of the new Spanish Structural Code (CE).
First of all, the service life table as a function of surface treatment details how corrosion resistance decreases as the exposure class increases. Knowing that all the structural elements must have a guarantee of at least 50 years of service life, the following table clearly shows that it can only be achieved with Electrolytic Zinc, Sendzimir Galvanized or Hot-Dip Galvanized as long as it is a C1 environment.
When it comes to a C2 environment, the only valid surface finish to resist corrosion for 50 years is Hot Dip Galvanized. From the C3 environment and up to C5, a surface treatment with more microns of protection must be carried out or opt to use stainless steel.
Continuing with stainless steels, the AISI304 steel option complies with most exposure cases except for HIGH category industrial and marine environments. On the other hand, the AISI316 steel option complies with all environments and exposure categories.